For some time now I have avoid using shell surfaces in the majority of my work as I have had trouble making them work in non-linear analysis for various reasons. Just recently I have had the need to use shell surfaces again and have come across a few issues -many I have had before. Perhaps some one may be able to help me with these?. First I have had success using *Tie connections between shells/shells and shell/solids but I get the red waring in MW26 suggesting that only solids can be used? (see attached pic).
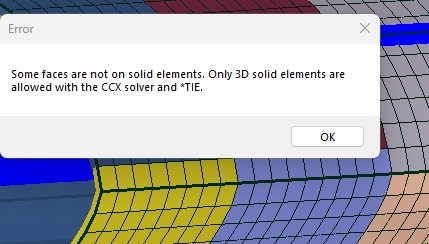
Is there any need to be concerned about that waring? Secondly I frequently can not run non- linear analysis (even if I relax the convergence tolerances). Is there a work around or is that some thing I'm doing wrong
Comments
*TIE kind of works sometimes but it's unreliable and I'm not sure what all the failure modes are.
Nonlinear analysis not converging is usually because of unconstrained rigid body but there are many reasons, buckling can also be one, or very large deformation, or contact too hard. You can run it as linear to make sure it's properly constrained, and if that doesn't help, delete big parts of the model, especially contacts, to isolate what's causing the problem. You can also add fixed supports to many parts to ensure no rigid body motion, then remove them until it fails.
Is it practical to extrude the shells to solids? The value of shells is that they're easier to mesh, not more accurate or faster to solve. CCX does the extruding internally but with a lot of ways to fails as you're seeing.